Water damage restoration with minimal disruptions at care home
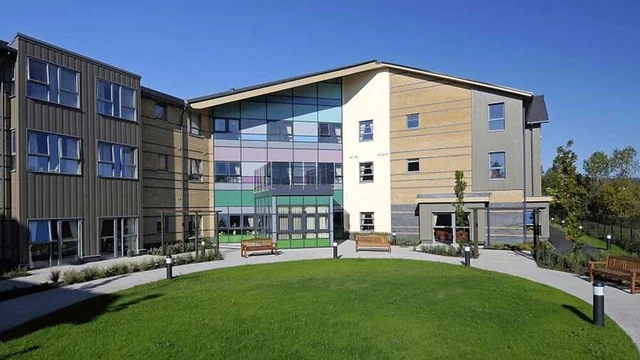
- Home
- Insights
- Humidity control and drying insights
- Water damage restoration with minimal disruptions at care home
In 2022, the Llys Glyncoed residential care home in Ebbw Vale, Wales, faced a critical challenge when an escape of water saturated the insulation layer beneath the screed floor. This water damage led to moisture wicking through construction materials, causing visible damage to the base of the walls throughout the entire building.
The timing of the water damage was particularly challenging as it occurred during the COVID-19 pandemic. With many elderly residents suffering from disabilities, relocation was not an option due to health risks. This created a need for a water damage restoration solution that was minimally invasive, allowing the care home to continue its operations with minimal disruption.
Implementing a health-safe and non-disruptive drying regime
In collaboration with our customer, Rainbow International South Wales & Bristol, we developed a tailored water damage restoration process to address the unique challenges and concerns at Linc Cymru. The key considerations for this project included:
- Trip hazards: Ensuring that residents, many of whom had vision impairments and difficulties walking, could safely move around the building without encountering trip hazards.
- Air quality: Maintaining a high standard of air quality was essential as the residents were susceptible to health issues from airborne contamination and damp conditions.
- Noise control: Since the care home was fully operational, minimising noise disruption was a key factor that influenced the choice of drying equipment.
- Isolated water damage: The water damage was isolated to specific areas, requiring a focused approach to avoid disturbing unaffected parts of the building.
- COVID-19 protocols: Strict COVID-19 safety measures were in place, including testing for visitors, which had to be considered in the restoration process.
- Temperature management: High summer temperatures and the well-insulated building posed a challenge in managing heat load during the drying process.
Targeted drying using negative pressure technology
Taking into account the above factors, a water damage restoration process was designed around a methodology of negative pressure (suction) drying setup, utilising the Aerial AERCUBE system in combination with condensation dehumidification and desiccant technology.
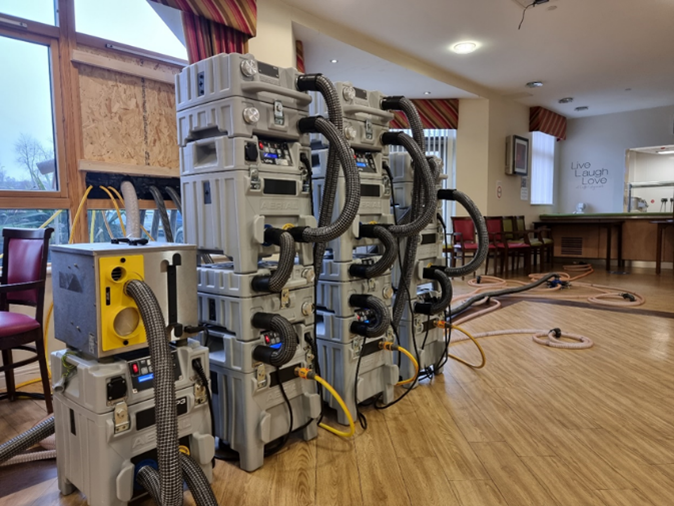
The ground floor was divided into two sections, allowing the care home to continue normal operations by relocating some key facilities to unaffected areas like the dining hall. This setup enabled the drying contractor to target approximately 50% of the affected area initially before moving on to the rest of the building.
![]() | ![]() | ![]() |
The Aerial AERCUBE system was selected for several reasons:
- Negative pressure setup: The ability to run in a negative pressure (suction) setup allowed for a targeted approach, whereas a positive pressure installation would have required drying the entire area simultaneously.
- Advanced filtration: The AERCUBE system is equipped with inline G4, H13 HEPA, and active carbon filtration systems, ensuring that moisture-laden air removed from the contaminated subfloor was free from bacteria, mold, and other harmful materials.
- Temperature control: The project took place during the height of summer and in a well-insulated building, with ambient temperatures being a significant concern. The drying equipment can only run up to 35°C, so managing the heat load from the drying process was a critical factor The AERCUBE system allowed for the venting of moisture-laden air and waste heat to the outside, keeping indoor temperatures under control and ensuring the drying equipment could operate effectively.
![]() | ![]() | ![]() |
Monitoring and managing the water damage drying process remotely
To further minimise disruption to residents and reduce the risk of COVID-19 transmission, Dantherm Group employed the Simplify remote monitoring system. This system allowed for real-time monitoring of the drying environment and remote control of the equipment. Various probes, including temperature, relative humidity, IAQ, and resistive probes, were used to accurately monitor drying performance and ensure that indoor conditions were safe and within the thresholds deemed appropriate for residents.
The remote monitoring system proved invaluable when a connection hose was accidentally moved during the drying process, rendering part of the system ineffective. The monitoring system quickly identified the issue, allowing a contractor to promptly correct the problem with an onsite visit, minimising downtime and project disruptions.
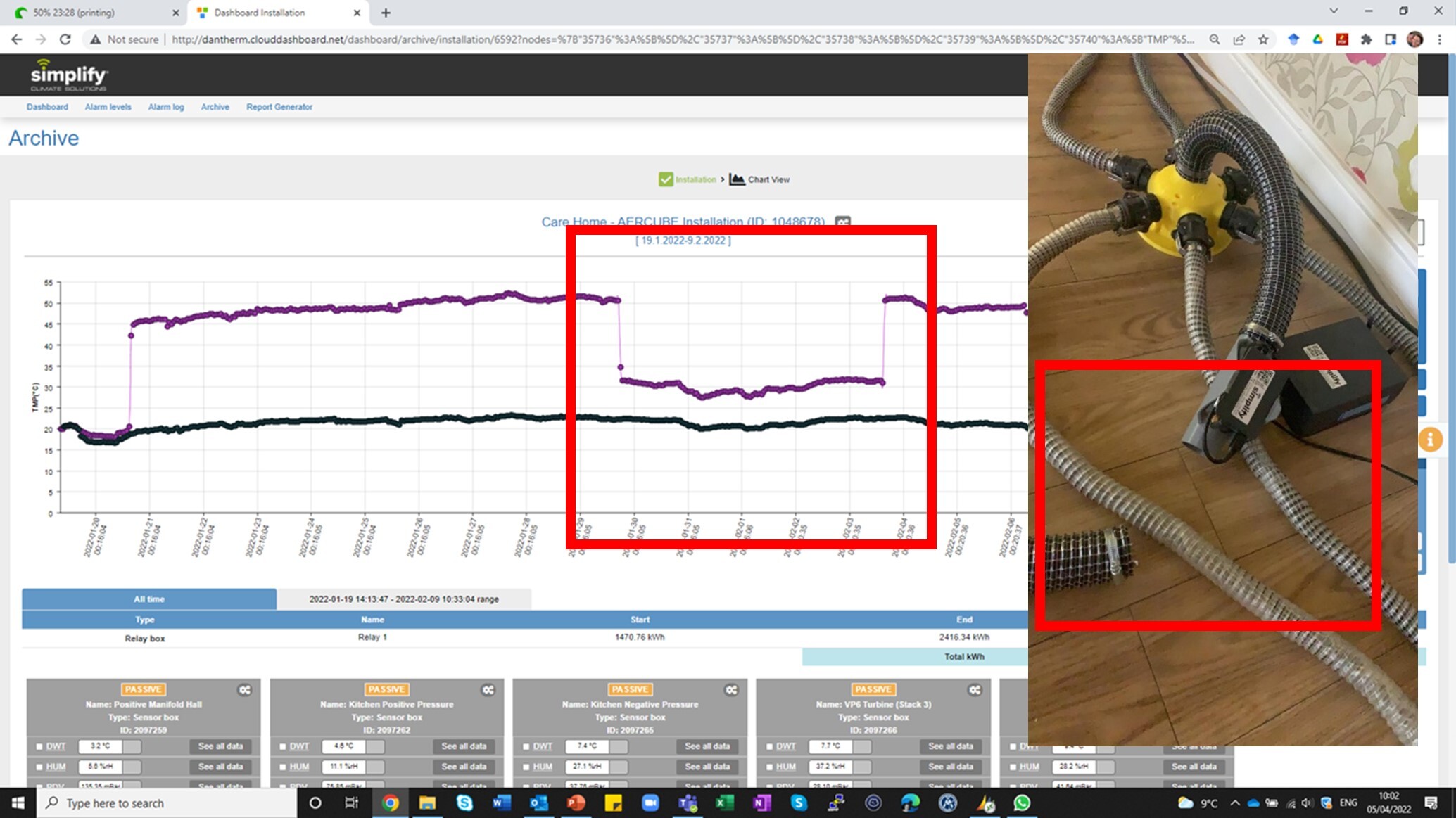
Successful project completion with minimal disruption
The entire water damage restoration project at the care home was completed within a four-week period, resulting in minimal business interruption. Notably, none of the residents had to be relocated during the project, and the restoration required minimal construction strip-out or reinstatement work.
This case study highlights the effectiveness of the Aerial AERCUBE system and the importance of a carefully planned, minimally invasive drying regime in maintaining the safety and comfort of vulnerable care home residents during a crisis.
Contact us
For more information on how Dantherm Group can assist with water damage restoration projects in care homes or other sensitive environments, please contact us today.
Related products
Featured insights
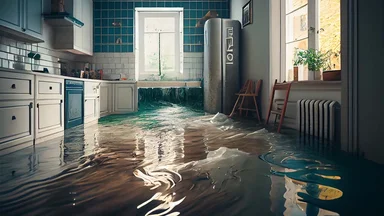
Discover everything you need to know about approaching a water damage restoration project.

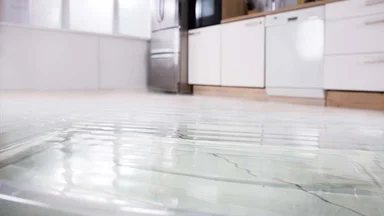
Explore the factors that raise the cost of water damage work for contractors – and where you can make savings.

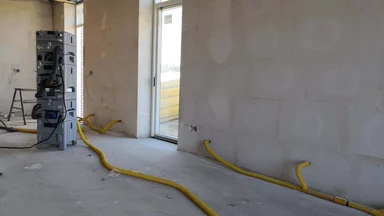
How negative pressure drying allows for targeted, safe drying of water-damaged buildings.

Need help with choosing the right solution? Our team of over 100 climate control experts can assist.
You can also reach out or join the discussion on our Social Media. Check out our LinkedIn page.