Stop moisture problems in your agriculture silo with dehumidification
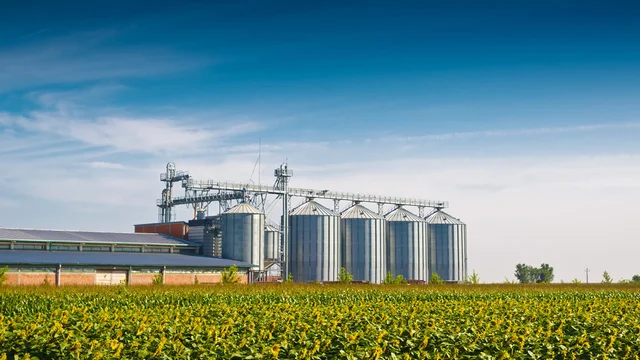
- Home
- Insights
- Humidity control and drying insights
- Stop moisture problems in your agriculture silo with dehumidification
Maintaining ideal storage conditions in grain and crop silos is a significant challenge – and one of the biggest threats to your stored products is the amount of moisture in these spaces.
High humidity, condensation and inadequate ventilation can cause numerous problems for your produce. Mould damage can destroy your crops. Grains clump together, making it harder and slower to remove from your silos. Water damage reduces the long-term integrity of your silos.
Controlling the humidity in your silos is vital to preserve your crops, maximise efficiency and minimise financial losses. In this article, we explain how agricultural humidity and drying solutions enable you to protect your goods and silos all year around.
The costly impact of high humidity levels in storage silos
High humidity inside storage silos can have extensive repercussions for your crops and overall farming operations:
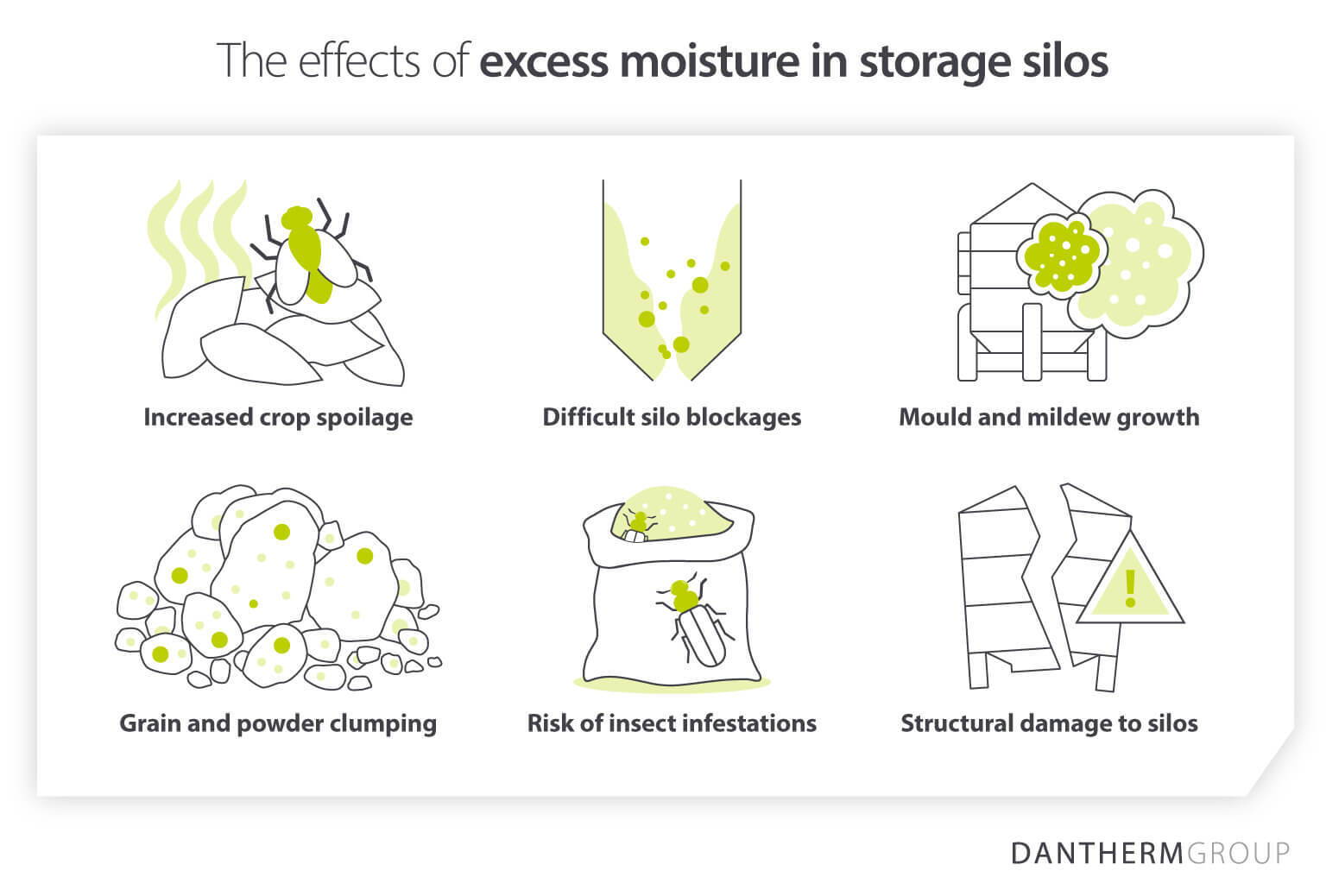
Crop spoilage
First, many crops, seeds and powders stored in agriculture silos are hygroscopic materials. This means they absorb moisture very quickly, which encourages microbial growth that spoils your crops.
Mould and mildew growth
Mould and mildew thrive in humid environments, and can quickly devastate entire batches of your crops. Mould growth may also cause regulatory problems and reputational damage if spoiled products enter the supply chain.
Silo blockages
Moisture causes grains and other stored products to stick together, creating blockages that reduce the efficiency of loading and unloading grain. Breaking up moisture-related blockages is often very expensive and time-consuming.
Grain and powder clumping
Grains with a moisture content of 18% or more are prone to clumping, making them harder to handle, process or package. This may force you (or your business partners) to discard or reprocess your goods.
Insect infestations
Moist, warm conditions in storage silos attract insects. Pest infestations can destroy crops, create health risks and lead to compliance problems. In addition, removing bugs from your silos is often very costly and time-consuming.
Structural damage to your silos
Persistently high levels of moisture can gradually corrode and weaken the structural integrity of your storage silos. Repairing this damage is expensive and requires disruptive downtime.
What causes moisture problems in agriculture silos?
Moisture issues in silos can arise from a variety of factors:
Fluctuating weather conditions: Temperature and humidity changes outside your silos can cause condensation on cool surfaces
Humid transport air from lorries: Warm, moisture-laden air during loading can condense inside silos when temperatures drop
Reverse jet cleaning of dust plants: Jet cleaning the top of your storage silos releases humid air into these buildings
Poor ventilation in silos: Poor airflow prevents moisture from escaping, causing humidity to rise in your agriculture silos
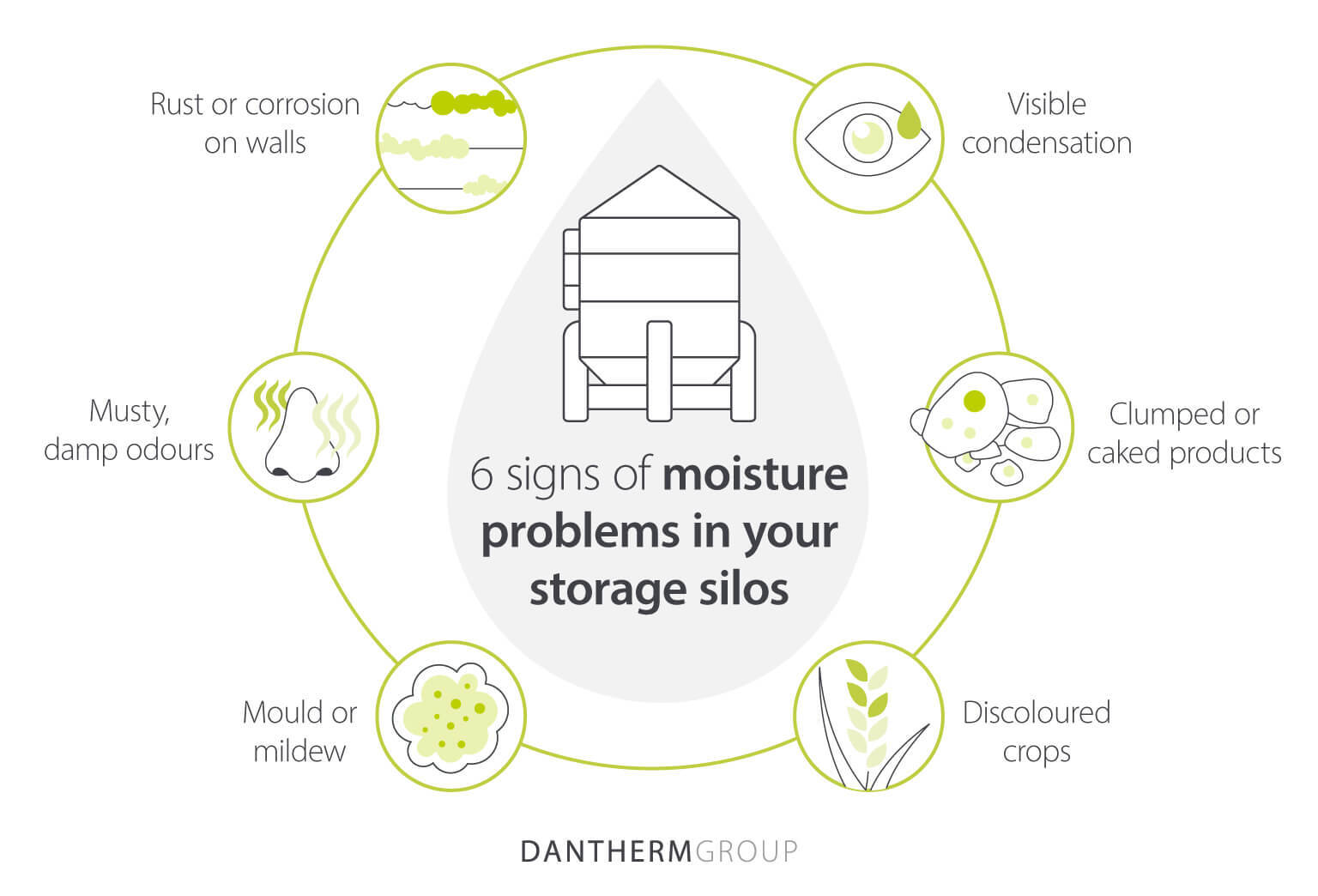
Industrial dehumidification systems: The best solution for silo moisture control
Many farming professionals have used aeration systems to tackle condensation in their agriculture silos. However, their performance is heavily dependent on the weather. In rainy seasons or tropical climates where humidity levels are consistently high, aeration systems may not work effectively.
For a more reliable solution for grain storage humidity control – regardless of the weather – you should use desiccant dehumidifiers. Desiccant dehumidification systems are designed to extract moisture from the air, ensuring stable, optimal conditions inside your storage silos.
How do desiccant dehumidifiers ensure humidity management in silos?
Desiccant dehumidifiers operate by passing humid air through a slowly rotating silica gel rotor. The gel absorbs the moisture from the humid air, meaning dry air is discharged back into the silo.
The silica gel rotor is regenerated using dry air and heat, so it can continuously regulate the moisture levels inside your storage buildings. The moist air is exhausted outside through a duct, meaning it cannot harm your crops.
With the right desiccant dehumidification system in your storage silo, you can:
Prevent crop spoilage in your silos
Restrict mould growth
Minimise blockages
Extend storage times
Reduce the risk of insect infestations
Preserve the structural integrity of your silos
Introducing a dehumidification system for your agriculture storage silos
For large, bulk agriculture silos, an industrial dehumidification system can be installed in a small enclosure next to the lorry loading pipe. A coupling connects the system, allowing for easy disconnection when loading grain, crops or other goods into the silo.
After installing the desiccant dehumidifier and attaching it to the loading pipe (or a standalone dry air pipe), the tube runs up the outside of the silo. Dry air is delivered into the ullage space – the area above your stored products – from the top of the silo.
By keeping the relative humidity in the ullage space at a safe, comfortable level, this stops mould growth from harming your crops, and prevents grain clumping together and creating blockages.

Selecting the right dehumidification system for your silo
To prevent condensation and preserve crop quality, there is no substitute for an effective desiccant dehumidifier. But, with many options available, how do you choose the right-sized solution for your site?
The ideal option depends on several factors:
The size and capacity of your silo
The material your silo is made from
The type of crop or grain you store
The outdoor climate conditions
It is critical to get this right. If your dehumidifier is not powerful enough to control the humidity within your silos, moisture damage may still affect your hygroscopic crops. If the dehumidifier is too powerful, this can over-dry your silo, damage your crops and increase running costs.
At Dantherm Group, our decades of experience designing and supplying dehumidifiers for the agriculture sector means we can find the best solution for your needs.
We tailor every solution to meet the specific needs of our customers. We examine the unique layout and structure of your sites to ensure that our solution fulfils your requirements in the most dependable, effective way possible.
Discover energy-efficient silo solutions at Dantherm Group
Dehumidification systems are non-negotiable means to safeguard your crops. If you want to learn more about dehumidification, our experts are here to help.
Dantherm Group is the European leader in agricultural climate control solutions. Backed by decades of expertise and the highest engineering standards, our dehumidifiers deliver total humidity control with minimal running costs.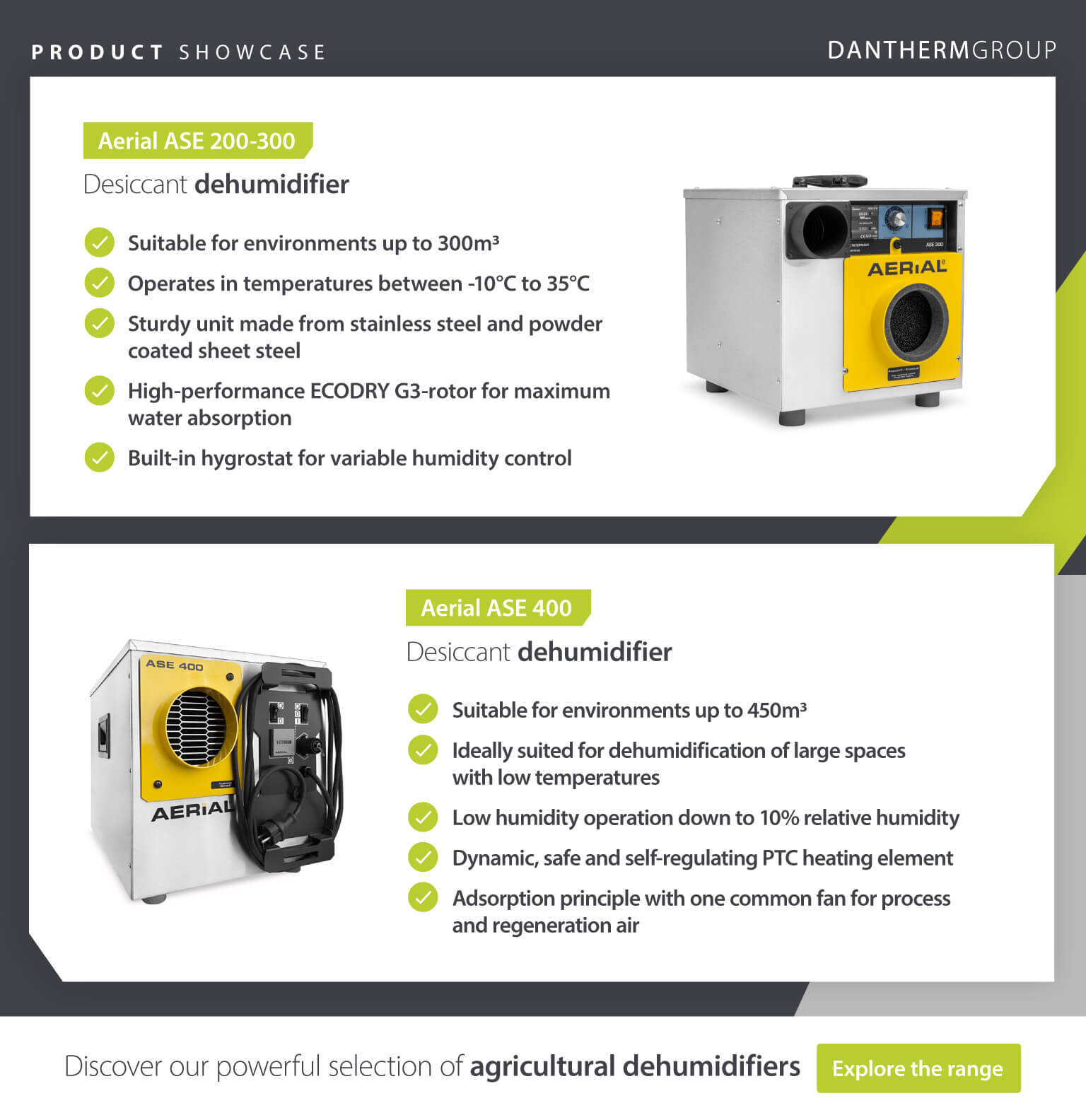
An extensive range of industrial dehumidifiers, delivering thousands of cubic metres of dry air per hour
Outstanding energy efficiency through in-built heat recovery systems and high-performance EC fans
Numerous customisation options to suit different silo sizes and crop types
Cutting-edge technology built for durability, reliability, usability and sustainability
An international supplier network that streamlines purchases and cuts handling costs
A bespoke, consultative approach – solutions crafted around your unique needs
Talk to the climate control experts in agricultural storage – reach out to our experts to discuss our dehumidification solutions.
Related products
Featured insights
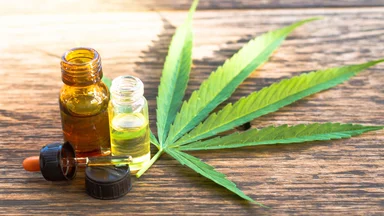
The key to consistent cannabis growth is a well-specified dehumidification system

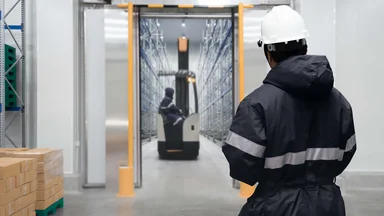
Regulating humidity can save you a whole host of problems

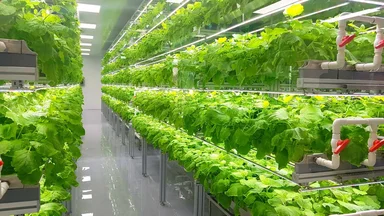
How regional farmers can take advantage of agriculture’s most promising innovation.

Need help with choosing the right solution? Our team of over 100 climate control experts can assist.
You can also reach out or join the discussion on our Social Media. Check out our LinkedIn page.