How much does it cost to dry out water damage?
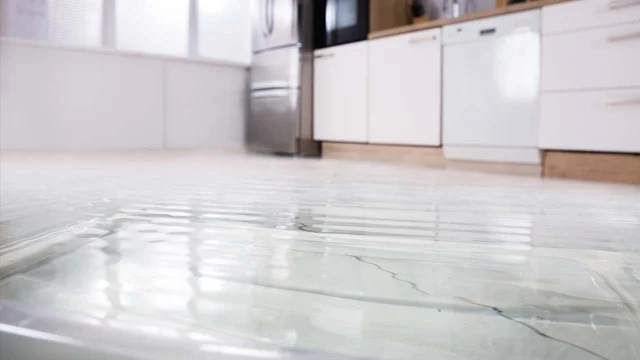
- Home
- Insights
- Humidity control and drying insights
- How much does it cost to dry out water damage?
Although insurers typically pay contractors flat rates or m2 rates for most water damage restoration projects, the costs for contractors can differ significantly. Here we discuss factors that influence the overall value of a project and how to keep these to a minimum.
There is no definitive answer to the cost of a water damage restoration claim. In domestic properties, insurers will often work based on the number of rooms affected and extent of the damage within these.
For projects involving the restoration of higher-value properties, such as stately homes and listed buildings, the value of a claim can be significantly larger, extending into tens of thousands of euros.
However, that is simply illustrating how much a contractor will be paid for the hugely variable scope of water damage restoration work they conduct. For the contractors themselves, the costs they incur on a project will depend on several factors:
The source and extent of the damage
Say a bucket of water is spilt or the taps are left running. This damage can be easy to spot and correct and, as a result, these types of jobs are simpler and typically less costly. Some will not even amount to a ‘worthwhile’ claim when you take into account policyholders’ excess insurance costs.
However, burst pipes or leaky roofs can cause the build-up of moisture in hard-to-reach places, such as cavity walls, voids, or insulated construction types. The structural damage these can cause may be severe, increasing the cost to complete the job.
The scale of the damage
As well as the number of rooms or areas impacted by water damage, it will also be important to consider the size and layout of the rooms affected. This will influence how many drying units, dehumidifiers, heaters and more will be required to dry the damage.
This also takes into account damage done to furniture, fixtures and other items beyond water ingress in the structure of the building itself.
The classification of water inside
The type of water found inside a property can influence the time it takes to complete a project, as well as the complexity and overall cost to complete.
Category 1 water, otherwise known as clearwater, has no impact on drying timelines. It is non-toxic and safe for both residents and contractors to live and work near.
Category 2 water, also known as grey water, can be toxic and have a moderate impact on project costs. Decontamination is a must and additional strip-out work may be required.
Category 3 water, referred to as black water, contains sewage backup and hazardous bacteria. This classification demands special safety equipment as well as post-drying decontamination and remedial work, often making this the most costly type of work.
The remediation processes required
In many cases, water ingress can damage hard-to-dry materials, such as hardwood floors, insulation in cavities and valuable ornate features such as architraves or wood panelling. Not only do properties need to be dried out, but strip-out work is often needed, adding to project timelines and costs.
In addition to delaying the payout from insurance companies, post-dry repair work can directly impact project costs, as contractors must remove and dispose of tarnished materials in a safe, ecological way.
Water drying costs contractors may overlook
The above are among the most obvious costs involved in a water damage restoration project. However, there are several other actions that water drying professionals take that add to their overall expenses – ones that they may not immediately consider:
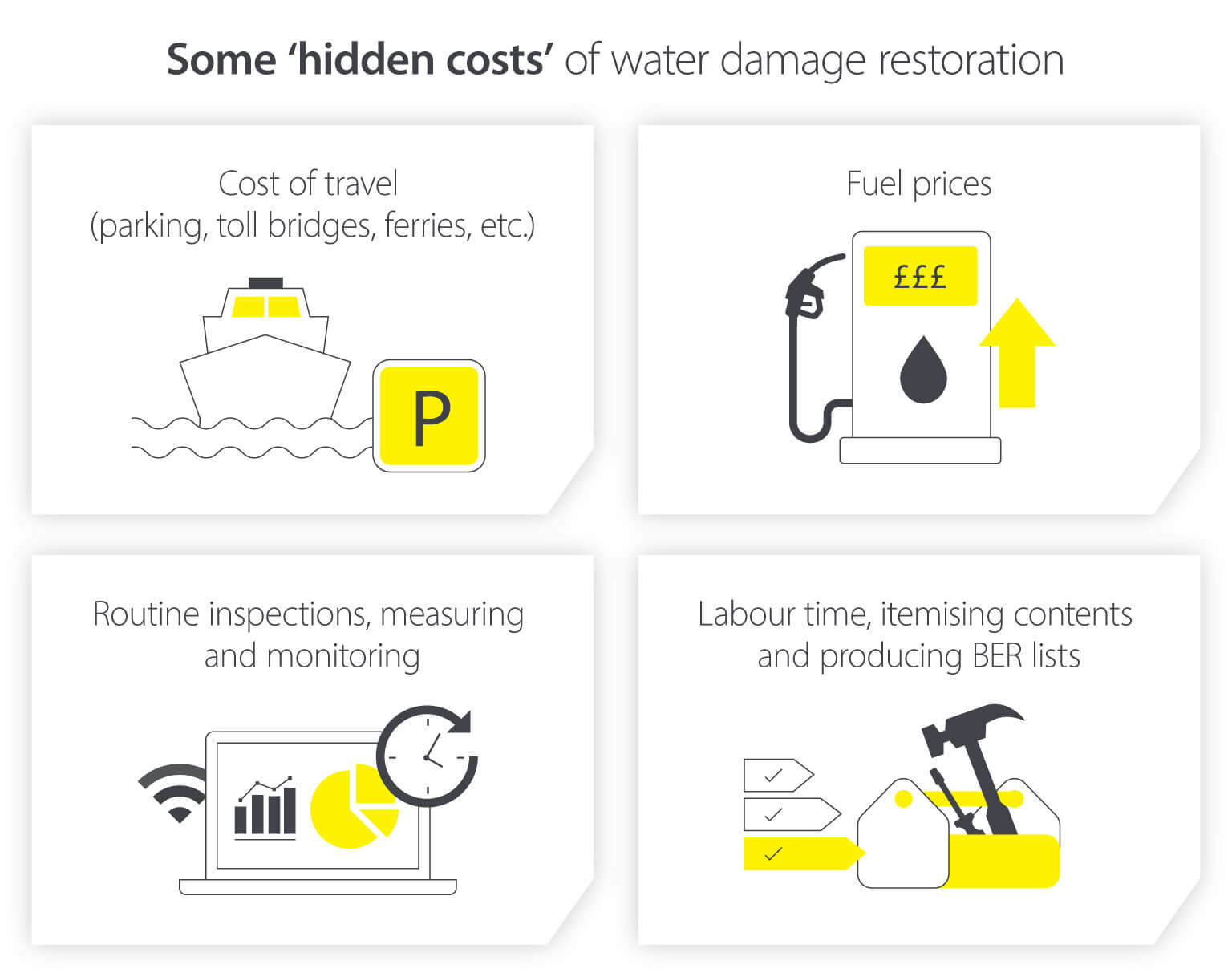
Every unnecessary visit to a drying site or ineffective setup does not just cost valuable time, it also uses up fuel and occupies teams that could be better spent elsewhere. Scale these costs up across a whole organisation, and it is clear to see the savings that could be made with a more considered approach.
How to minimise water drying costs
Invest in small, compact equipment
By opting for smaller easy-to-transport equipment, such as the AD 20, teams can accommodate more units in their vehicles. This means they can attend more sites in one round of travel rather than repeatedly going back-and-forth to a depot to reload equipment.
While these compact condensation dryers have less water removal capacity than larger units, they represent an energy-efficient and effective way to resolve water damage in most small to medium-sized domestic claims. This also pays dividends for your company’s carbon footprint.
Of course, some projects may demand a larger, more capacious unit. However, where possible, opting for compact, trusted units will serve you well and provide a scalable solution.
Remotely monitor progress
Rather than spend valuable time and money sending technicians to sites for manual checks, investing in remote monitoring technology allows your team to track performance from the comfort of your offices.
This approach can quickly identify if and when units require maintenance or a physical inspection, rather than travelling to the site on a rota, which can be an incredibly inefficient use of resources.
Monitoring solutions also highlight equipment downtime, such as when a homeowner gets frustrated by the disruption caused and switches everything off. How many times have you arrived on site only to find that your equipment has been turned off since Day 1?
In addition, fewer visits from technicians means less disturbance for people living or working on-site while the project is carried out.
Employ targeted drying
By investing more time at the beginning of a project to set up targeted technology, teams can expedite water damage repair jobs by as much as two weeks in larger cases.
Projects are completed and invoices are paid sooner at the cost of a few additional hours at the beginning. Whilst this isn't an obvious benefit to a technician, it certainly pleases the accountant when the cashflow situation improves.
Furthermore, targeted drying limits the risk of secondary damage occurring within the property.
Acquiring equipment that’s built to last
While there is always the temptation to minimise upfront costs on equipment, especially in an industry where margins are incredibly fine, buying a reliable, well-built unit from a trusted brand is far more profitable for water damage contractors in the long run:
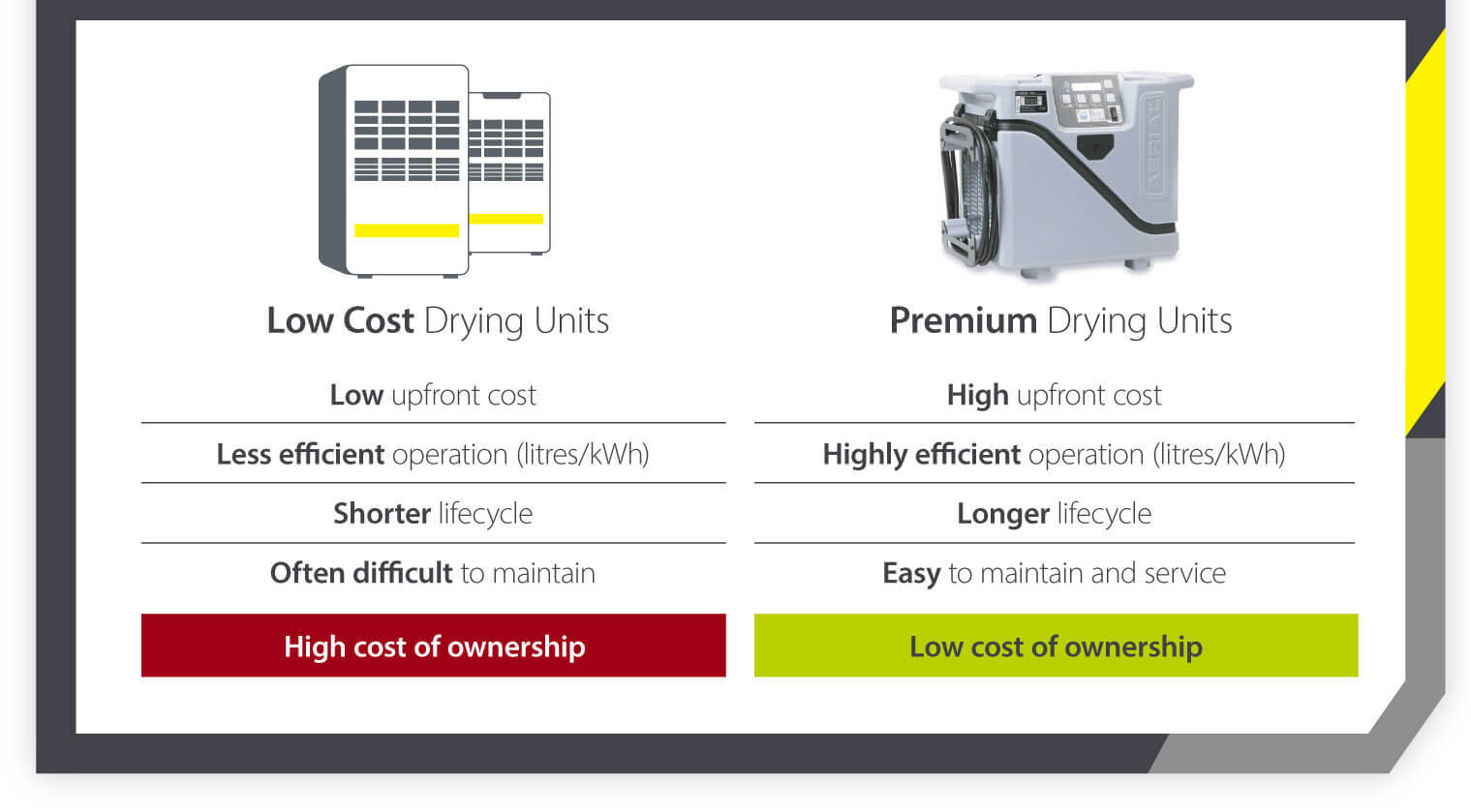
Of course, not all of these tips will be possible on every single site. However, implementing even just a few of these tips across a fraction of contracts can generate significant savings.
Inappropriate ways for contractors to make savings
While there are numerous different ways professionals can limit water damage restoration costs, not every aspect of the drying process should be optimised…
Spending less time during the initial setup phase so you can move on to the next job sooner may extend the length and complexity of a project by days or weeks – including a greater risk of more severe damage and costly remediation work.
Similarly, while purchasing low-cost, low-quality drying units may provide short-term savings, in the long term these will be more expensive to operate and maintain, and have shorter lifespans. Buying quality from the outset will save you more in the months and years ahead.
Remember that poorly conceived ‘savings’ are not only financial, but also impact on your reputation. If you become known for minimising investment in equipment and training, and this reflects in overrun projects, poor results and unhappy customers, it affects your ability to attract ongoing work.
Why water damage professionals trust Dantherm Group
Every drying project is unique and the cost to complete a single job can vary significantly. To help minimise expenditure and maximise margins, Dantherm Group provides a wide range of high-performance drying technology suited to every scenario.
Professional dehumidifiers for water damage drying capture and remove moisture from the air to aid the drying process. The best mobile dehumidifier setups for water damage restoration can generate exceptional results and hasten projects.
Pressure drying systems drive hot, dry air into affected areas to aid the extraction of moisture from saturated materials hidden within enclosed spaces such as cavities. This modern approach to drying can be used to great effect on-site in a number of scenarios.
Negative pressure drying – also known as insulation or suction-drying – provides a controlled, effective way to capture and remove water damage hidden in wall cavities and subfloors, with minimal risk of contaminating the air. Suction drying also offers much more control over the drying process for technicians operating in domestic dwellings.
Units such as the AD 20 are not only effective condense dehumidifiers, they are also easy to maintain, built to last, and highly energy-efficient – ideal for many situations.
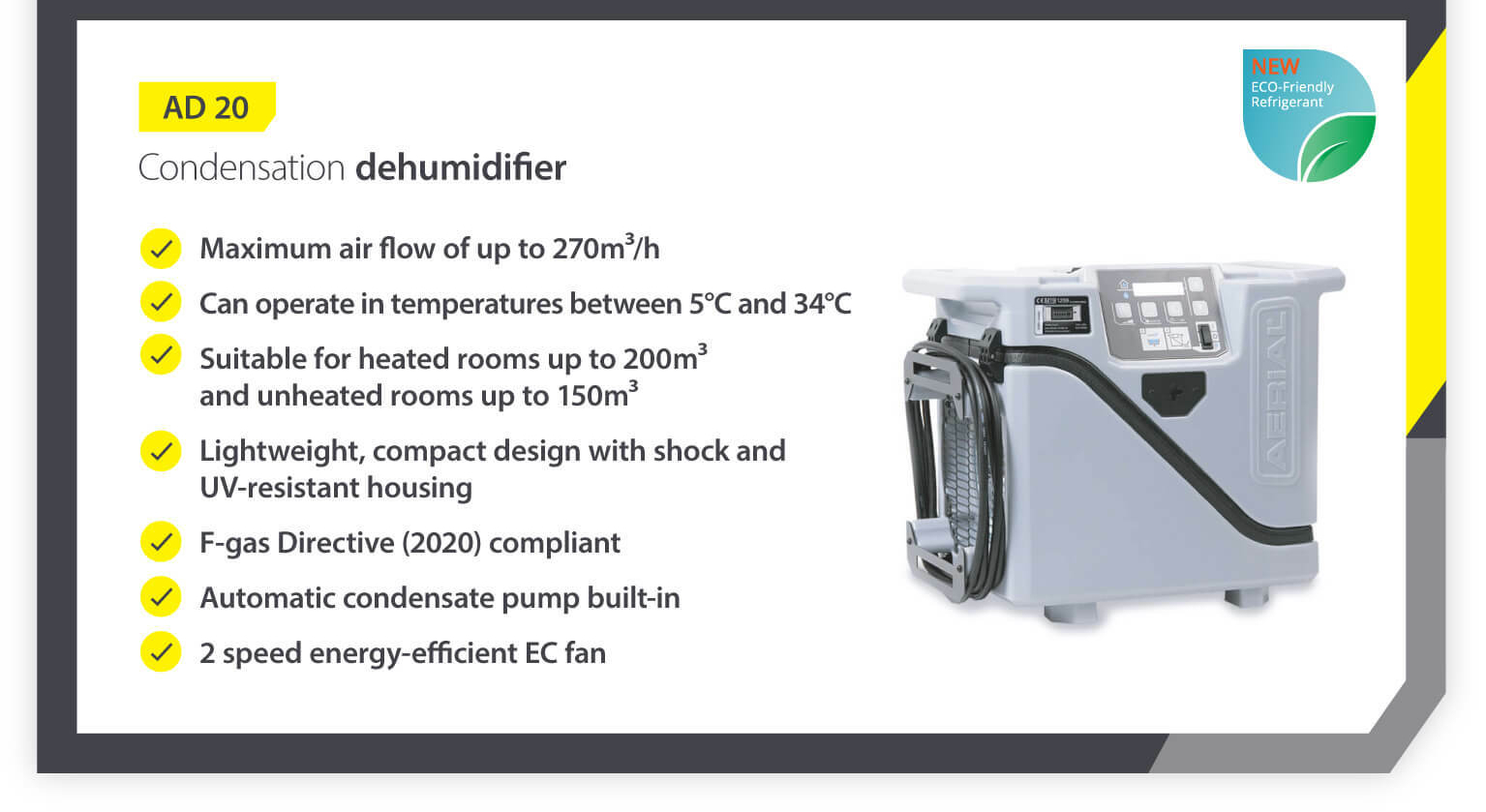
It is not just the sheer variety of our lineup or our vast expertise that makes our technology the go-to solution for water damage professionals – we focus on four key areas:
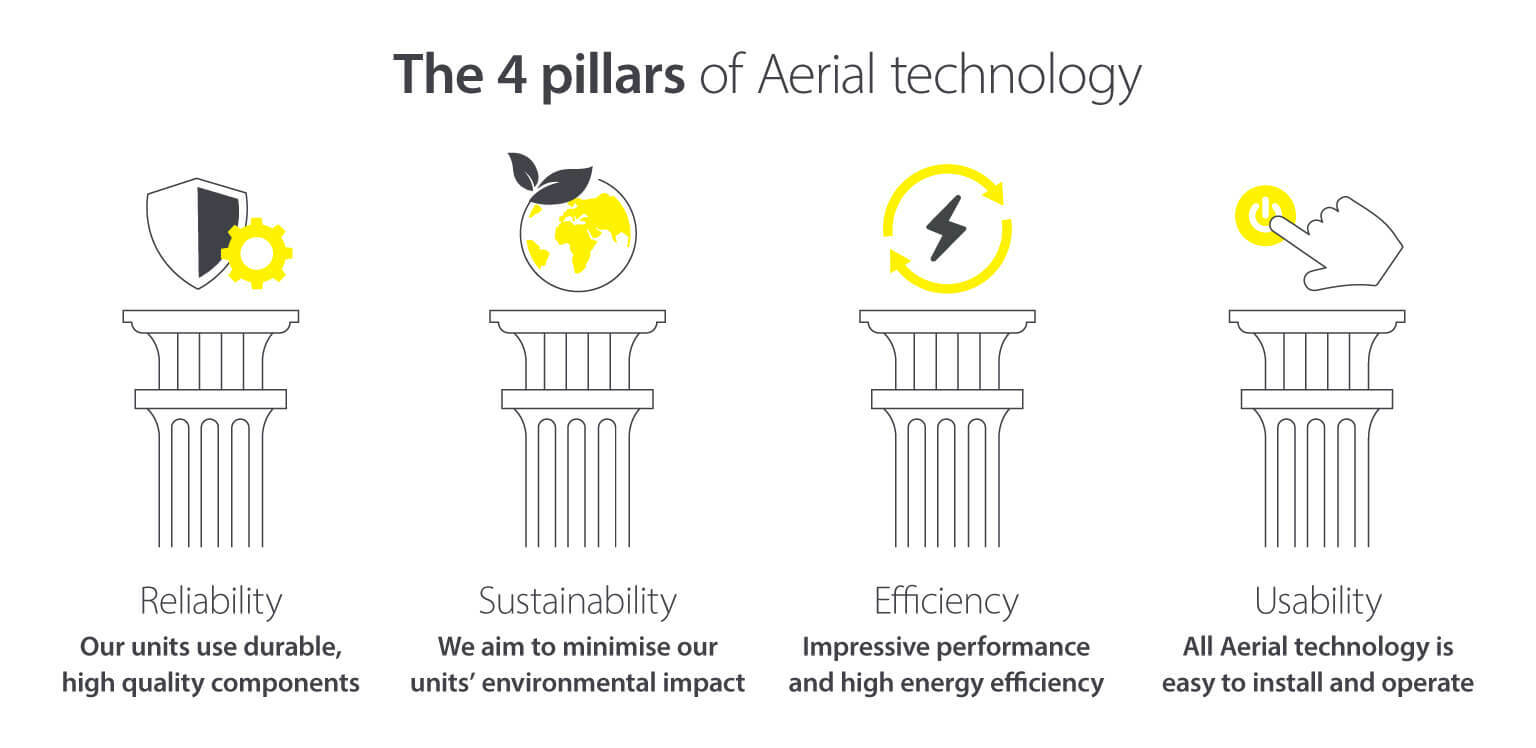
Our drying systems are backed by our vast support network, placing expertise, spares and advice a single phone call away. We also deliver concentrated training, guidance and advice to all customers so you and your teams get the absolute most value from your drying equipment.
If you would like to learn more about our drying systems, get in touch online or by using the form below.
Related products
Featured insights
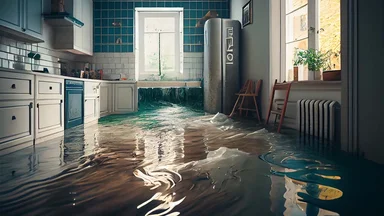
Discover everything you need to know about approaching a water damage restoration project.

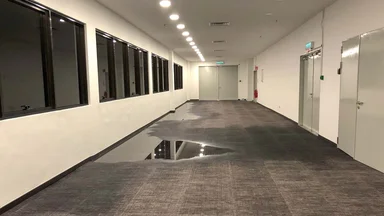
Explore the factors that influence the amount of time it takes to dry water damage, including the equipment you use.

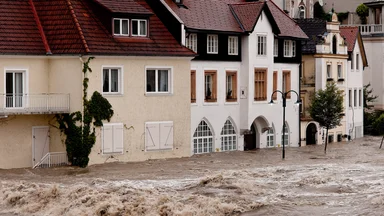
Explore the core areas of restoring a property following a flood - managing air quality, controlling the climate and building drying.

Need help with choosing the right solution? Our team of over 100 climate control experts can assist.
You can also reach out or join the discussion on our Social Media. Check out our LinkedIn page.