Energy-efficient climate control for the fish processing industry
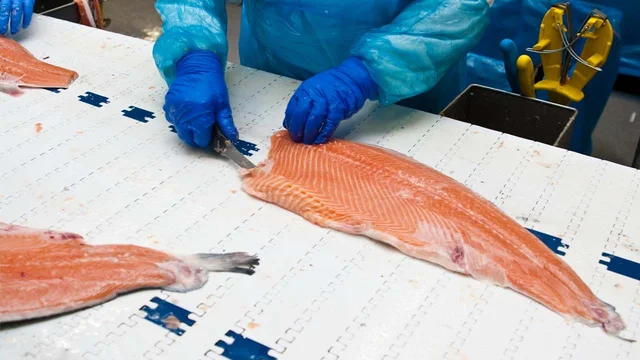
- Home
- Insights
- Humidity control and drying insights
- Energy-efficient climate control for the fish processing industry
Energy costs are a hot topic for fish processing plants, who can potentially spend a lot of electricity to maintain optimal climates at all times. Below, we explain how Dantherm’s ECOline solution is significantly reducing the energy demands of climate control in this industry.
Fish farming, seafood processing and other forms of aquaculture are crucial to supplying people across the globe with fresh fish. With the growing number of land-based facilities managing the farming, butchery, filleting and storage of fish worldwide to meet ever-increasing demand, the need to achieve consistent indoor climates at all times is of paramount importance.
Why is climate control for fish processing important?
In a previous article, “How dehumidification is modernising Norway’s fishing industry”, we highlighted how critical it is to use a combination of desiccant dehumidifiers and ventilation control systems to keep the temperature, humidity and air quality in fish processing plants optimal. Without effective climate control, there can be notable negative consequences:
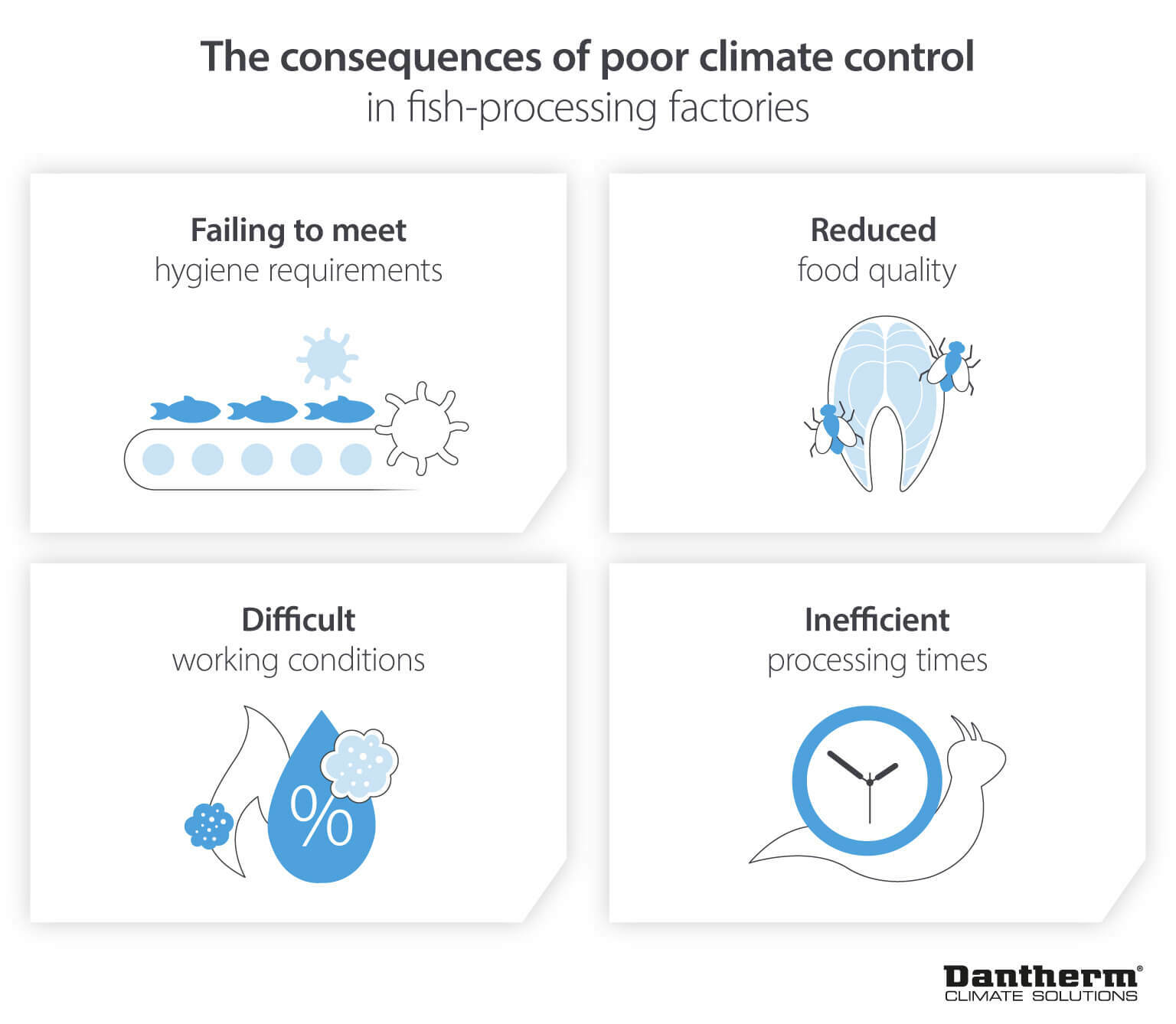
This is particularly prominent in locations like fish processing factories due to the low temperatures and moisture levels that must be maintained for the fish quality (between 8ºC and 12ºC and max. RH% 45).
There is a lot of excess water in the summer when hot humid air is brought into these low temperature/humidity conditions, and also a significant amount of cold water is used during operations. If temperatures and humidity are allowed to rise uncontrollably, it can lead to dangerously high moisture levels.
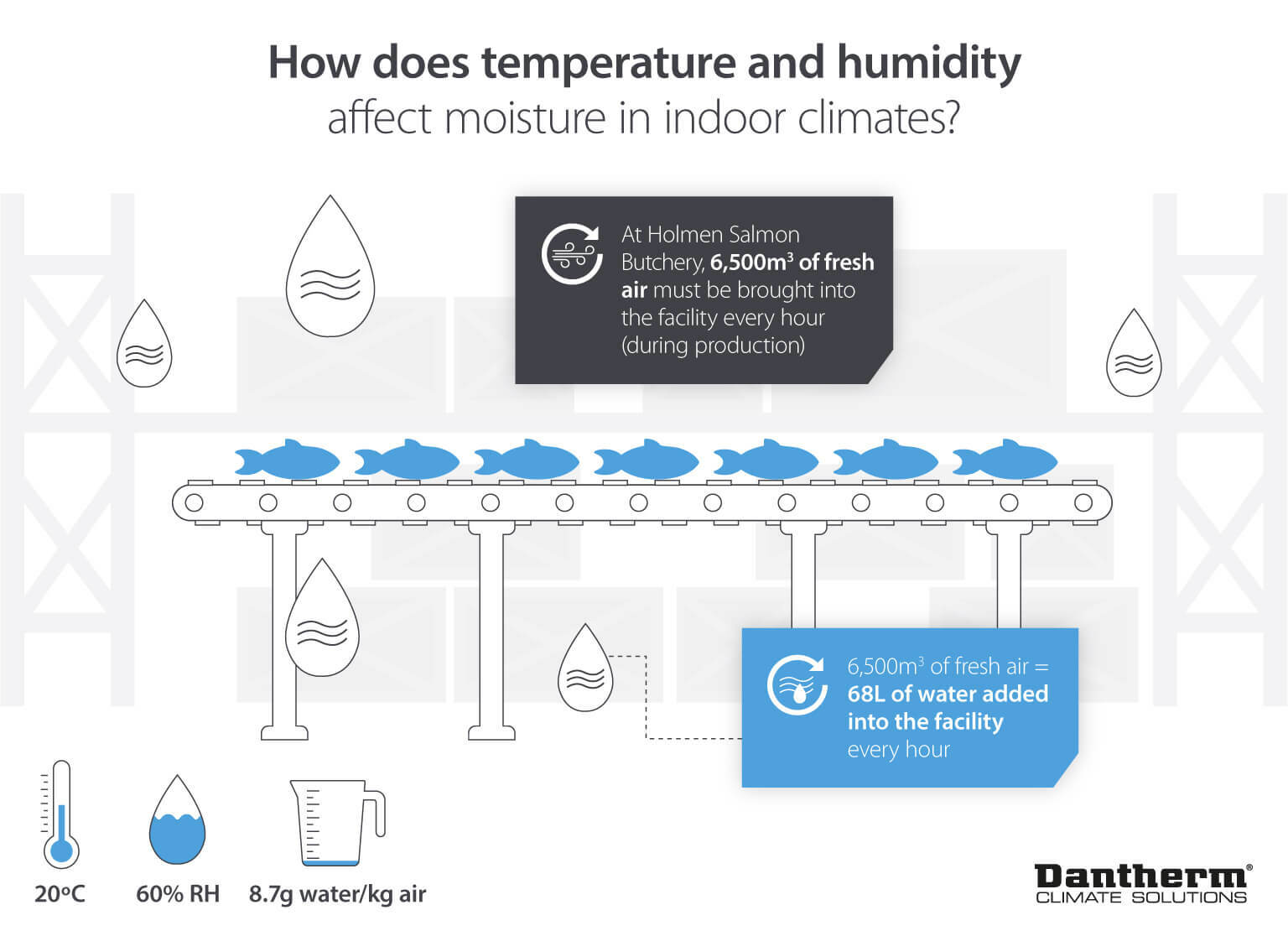
Precise dehumidification and ventilation keep the climate within acceptable boundaries throughout the various stages of fish processing. Using the right solution, the quality of fish is preserved, work can be conducted much more efficiently, and there is a greatly reduced risk of breaching hygiene regulations.
However, traditional desiccant dehumidifiers are known for high levels of energy consumption. Even though a condense dehumidifier unit consumes less energy in warmer temperatures, it is not effective in low temperatures and will not be able to maintain the demanded RH% at the low temperatures that must be maintained in the fish processing industry.
Drying with fresh air only or with a condense dehumidifier is therefore not an option and the desiccant dehumidifying process has the potential to use a lot of energy. And, at a time where energy prices are surging across Europe, this is understandably a key concern for fisheries.
Dantherm has recognised this problem for a while, which is why we have always worked to make our dehumidifiers and air handling units as efficient as possible. And now, we have taken this a step further with the Dantherm ECOline solution – ensuring the fish processing and seafood industries can keep climate under control, and substantially reduce their energy spend.
How the Dantherm ECOline helps create sustainable fisheries
The ECOline is a specially adapted version of our DanX CF air handling unit – already a very effective air dehumidification system with a highly efficient contraflow heat exchanger.
In the ECOline solution, the DanX CF is combined with an SD adsorption dehumidifier. In some applications this is a good and energy-effective solution without anything extra. In other applications, we are utilising ice water in order to both cool down the air entering facilities, and utilising the surplus heat from the ice and ice water production to significantly reduce energy consumption.
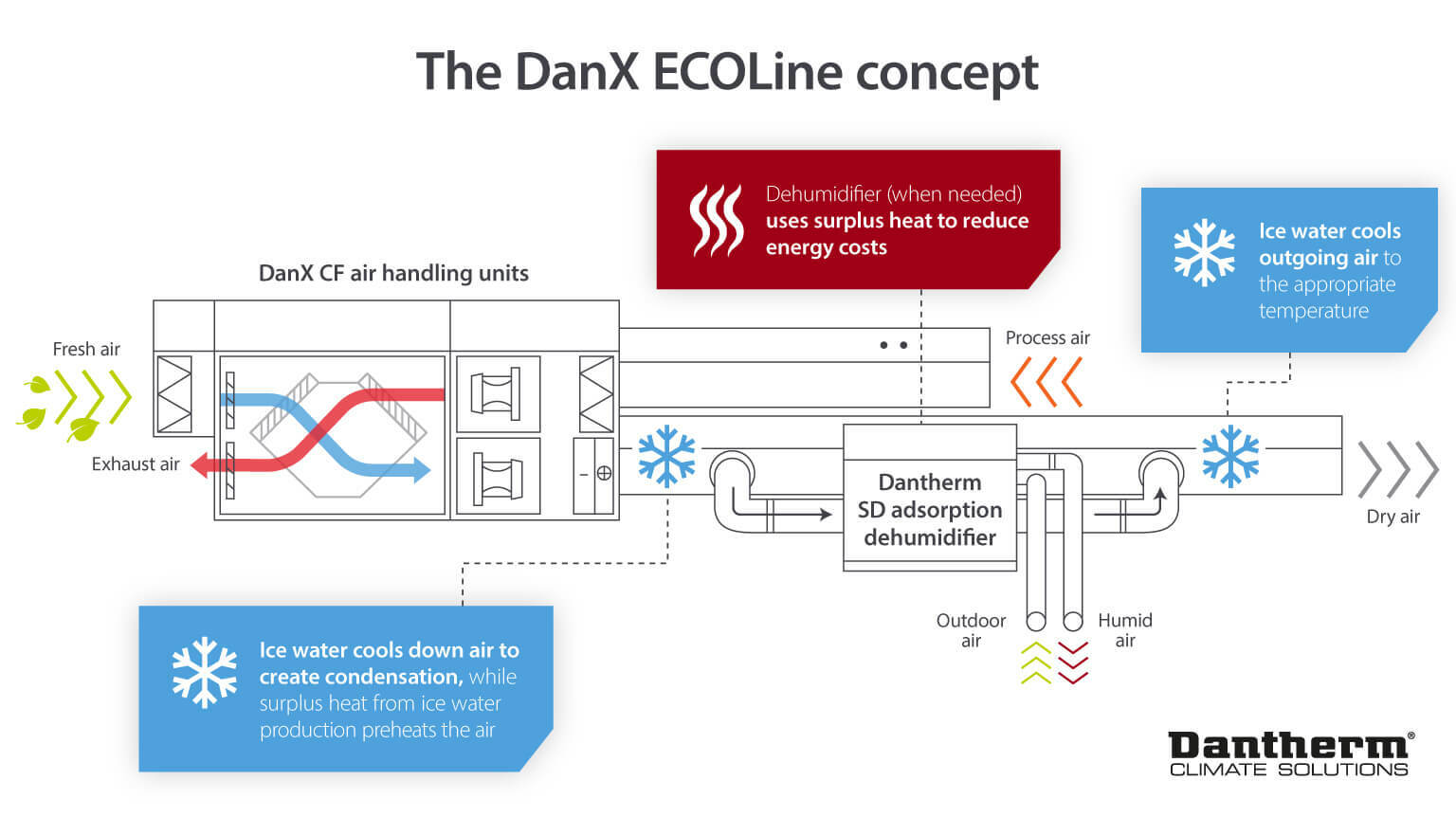
More or less all industrial or office buildings are in need of cooling. Traditionally, a solution based on refrigerant gas is chosen. But it starts to be more common to use ice water based on CO2, propane or ammonia. This is a much more environmentally friendly solution and also more cost-effective. The process of producing ice water generates a lot of heat. Traditionally, this heat would simply be expelled outside, and for the most part wasted, but are utilised in the ECOline concept in several ways.
Any fish process industry delivering fresh fish also needs ice, ice slush and/or ice water. Even though an ice water solution used for the butchery process is cost-effective on its own, investors are recommended to plan a total solution with ice water production with capacity to deliver to all the facilities/processes needed at a site.
How does this work? Dantherm ECOline get supplies of ice water, normally at temperatures approximately 2ºC to 4ºC (other temperatures can also be used). This ice water is applied at the contraflow process in the DanX air handling unit, where the fresh air interacts with process air (air from inside the building).
There are 4 ways the solution helps to save energy:
1. Drying with outside air using a contraflow heat cooling exchanger and ice water
While the contraflow condenses the air to a degree, the ice water condenses the air even further, and this alone will generate enough dry air to reduce the humidity within the fish processing plant for most of the year.
This is incredibly efficient, as this system means that the desiccant dehumidifier included in the Dantherm ECOline is only operating when it’s absolutely necessary to do so.
2. Desiccant dehumidifiers with surplus heat
When the desiccant dehumidifier is needed, the surplus heat, generated at no additional cost from the ice production, is used to dry out the moisture from the rotor in the specially designed SD rotor dehumidifier, which would otherwise need to be heated using expensive electricity, gas or other energy sources.
Therefore, the energy cost associated with a powerful desiccant dehumidification system is drastically reduced all year round, saving fisheries substantial sums over time.
3. Post-heating process air with surplus heat
When the ice water condensation is enough and the desiccant dehumidifier is not operative, the process air will be as low as 5-6ºC, and need to be post-heated (using the surplus heat from the ice water process) to achieve a temperature slightly below the process room temperature (or lower if further cooling is needed).
4. Post-cooling the process air with ice water
Furthermore, when the desiccant dehumidifier is in operation, the ice water will effectively cool down warm air produced as a result of dehumidification, so the dry air entering the facility remains at the cool temperatures required for optimal performance.
Again, by harnessing this surplus heat energy rather than letting it go to waste, this reduces the energy demands of the system, increasing its energy efficiency even further. The result is significantly reduced energy consumption, while keeping the climate during all stages of fish processing exactly as it should be.
How does this solution support the stages of fish processing?
There are multiple stages involved in fish and seafood processing.
When the fish is farmed, the process continues indoors:
Gutting and filleting the fish
Washing the premises in order to maintain hygiene standards
Drying the area following washing
Storing, refrigerating and preparing fish for transportation
Each of these will demand different climatic conditions.
During normal operation (gutting and filleting the fish), the temperature will be kept between 8ºC - 12ºC, and the humidity no greater than 45% RH. Meanwhile, during and after washing the premises, you will want to ensure maximum ventilation and heating so the area dries as quickly as possible.
The Dantherm ECOline excels in keeping the air inside the building consistent and the relative humidity at a controlled level. The system can either automatically adjust its settings based on a factory's shift hours and working patterns, or someone can manually switch between the different modes.
Plus, this technology (unique control system) is intelligent enough to monitor the temperature and humidity both inside and outside a fish processing plant, and adjust accordingly to keep the climate inside within safe, acceptable levels at all times.
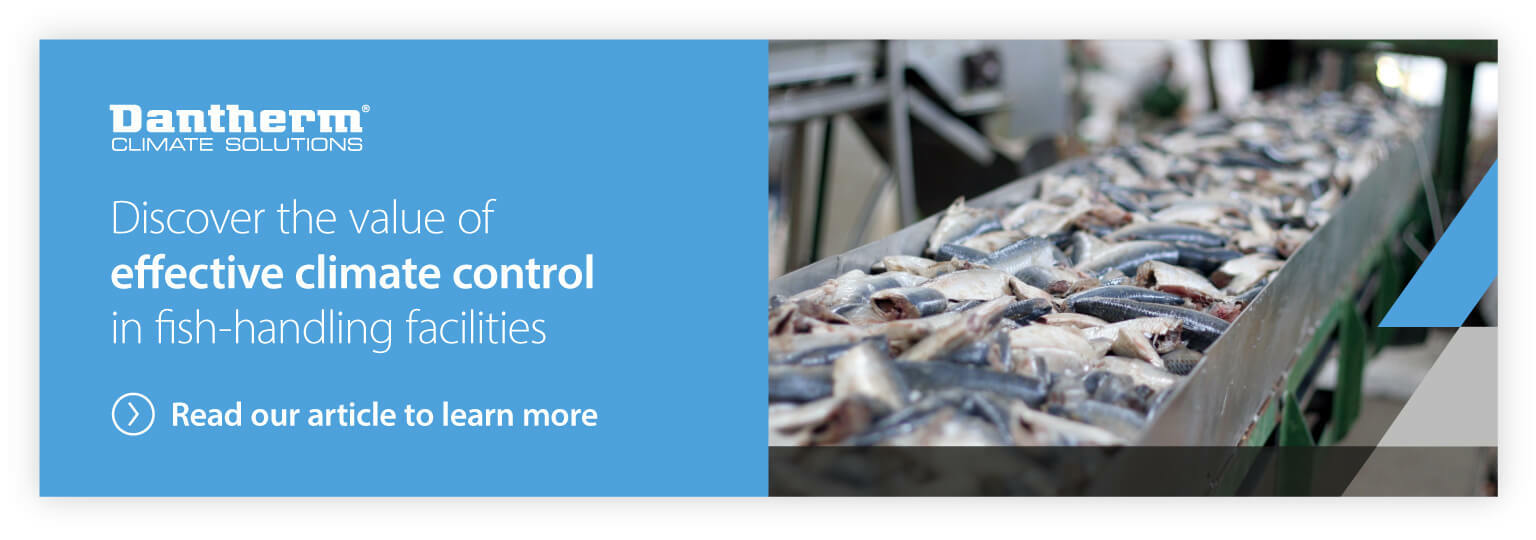
Are the energy savings worth the investment?
Any fish processing facility needs both a ventilation system and a dehumidifier to keep the climate at an optimal level and conditions comfortable for workers. The ECOline system provides both of these requirements in one, complete solution.
This can result in significant savings when compared with the cost of assembling and installing a separate ventilation system and dehumidifier. In addition, the reduced energy consumption associated with our technology and the use of ice water will generate significant cost savings across their lifetime.
On top of this, you receive a total package with one control unit, automatically controlling the conditions according to the processes at work and the outdoor climate. This all combines into a clever long-term investment for fish processing plants, especially for companies seeking to reduce emissions.
The ECOline in action: Holmen Salmon Butchery
To illustrate the potential of the Dantherm ECOline range, we would like to share a case study of how this climate management system has benefited Holmen Salmon Butchery in Sortland, Norway.
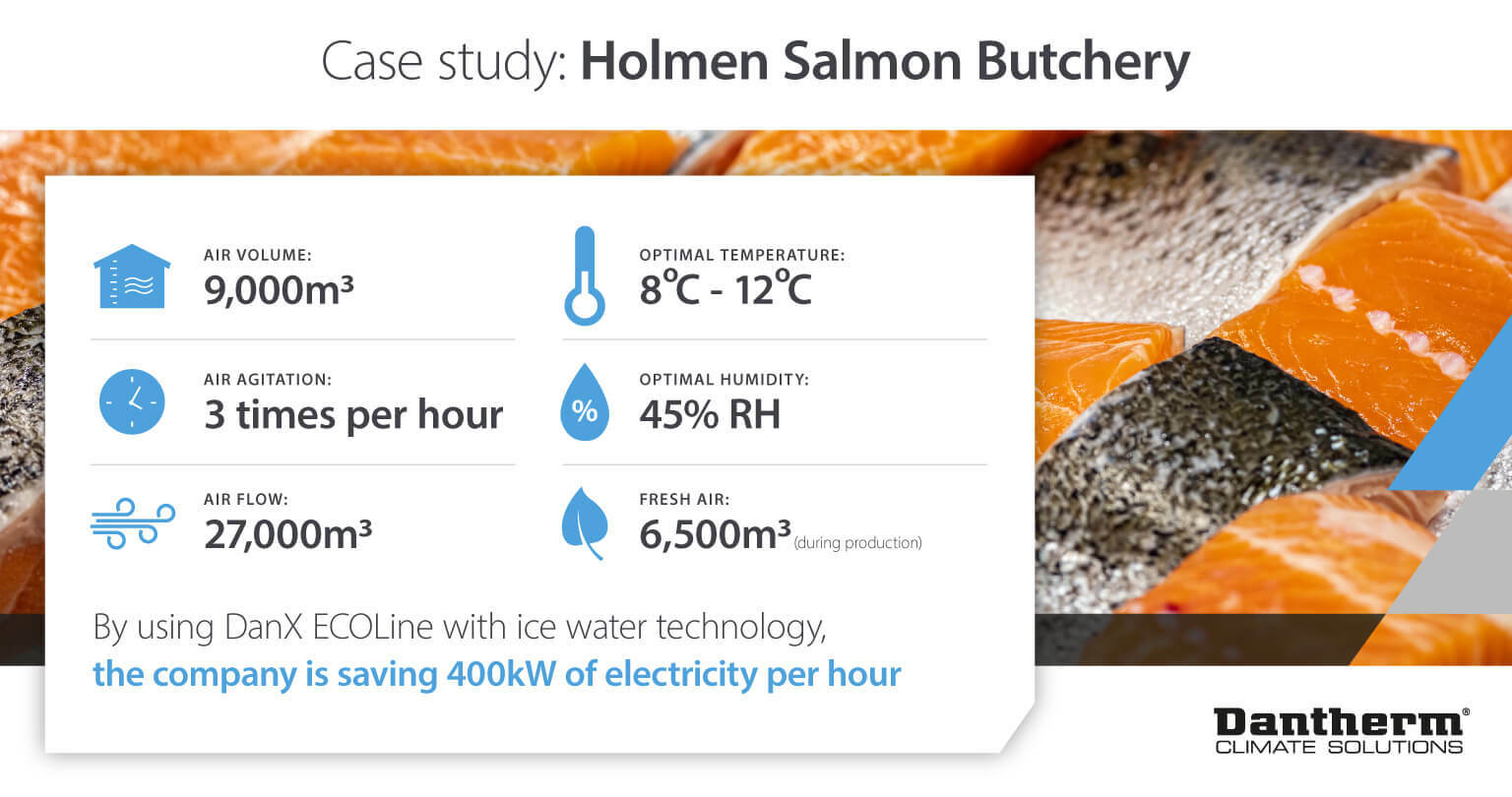
The company was seeking an effective climate control solution to keep conditions optimal throughout their facilities, and maintain comfortable conditions for their employees during operating hours. This entailed:
Indoor air volume of 9,000m3, with the need to agitate the air three times per hour – demanding an air flow of 27,000m3/h
Temperatures kept between 8ºC and 12ºC, and 45% RH
Up to 6,500m3 of fresh air during operating hours
Furthermore, during the summer months, the system would need to remove 8g of water per kg of fresh air in order to reduce the moisture load of the area (during the winter months, the drier outdoor air would dry the facility).
Our solution was to introduce three ECOline units to the premises, enabling the following:
Ideal temperature, humidity and air quality maintained across two 8-hour operating shifts, supporting work efficiencies, product quality and employee wellbeing
Maximum ventilation and heating to ensure premises were dried in under 2 hours after being washed (either with steam or a mix of hot water and chlorine), minimising downtime between shifts
No fresh air delivered between shifts (with no people present), allowing for more efficient air agitation
By harnessing this technology, Holmen Salmon Butchery saved 400kW an hour of electricity compared with a conventional desiccant dehumidifier, and ensured that the appropriate temperature and humidity were maintained at all times, minimising condensation and producing quality fish.
Discover the Dantherm difference
With ice water technology now a tried-and-tested possibility across the DanX range of air handling units, Dantherm is leading the way for more efficient, environmentally friendly food climate control across Europe.
While fish processing is one of the key industries to embrace this innovative approach to climate control, this technology is also being applied in numerous other settings, from state-of-the-art swimming arenas to extensive museum archives.
For over 30 years our experienced engineers have been experts in dehumidification, calculating the exact systems needed based on the size, scale and parameters of any fish production facility. By continuing to innovate and evolve our solutions, we are delivering better control, tighter processes and lower energy consumption for our customers across Europe.
Before you purchase any system, ensure you understand the return on investment you can achieve with Dantherm. Our team will be happy to talk you through it – contact us using the form below.
Related products
Featured insights
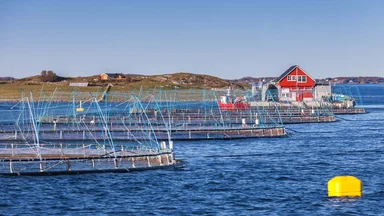
Streamlining fish processing techniques through climate-control technology.

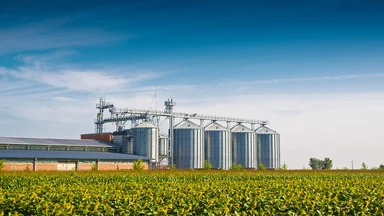
How to tackle moisture problems when storing bulk materials

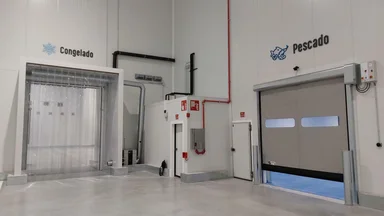
Read the story and learn how they also reduced their energy consumption and maintenance requirements

Need help with choosing the right solution? Our team of over 100 climate control experts can assist.
You can also reach out or join the discussion on our Social Media. Check out our LinkedIn page.