A guide to water damage drying
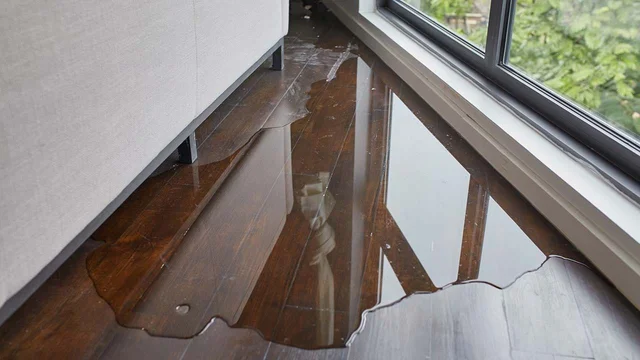
- Home
- Insights
- Humidity control and drying insights
- A guide to water damage drying
In many buildings, the water-bearing pipes are often in need of renovation due to changes in living habits, more airtight construction and an increased need for hygiene. Strong storms and increasingly heavy rainfall also contribute to water damage. Water damage restoration is of immense importance to prevent mould infestation. This can be done, for example, with the help of building dryers or by drying out the floor.
Causes of water damage
Water damage can have various causes. The most common cause is a burst pipe caused by corrosion, frost, construction work or a material defect. But floods, a defective washing machine or similar technical defects can also cause moisture damage. These must be treated quickly so that furniture, walls and floors are not damaged. This is where technical drying with drying devices and fans come into play to dry rooms and surfaces and to remove the moisture from the room air. Water damage is divided into:
Acute damage: The so-called water damage caused by burst pipes, rainwater intrusion, flooding, fire-fighting water and leaking appliances such as a washing machine.
Long-term damage: The so-called moisture damage caused by defective building seals, condensation on cold exterior walls and increased humidity in living spaces.
How do you dry out water damage?
Step 1 – Identify the cause
Before water damage can be repaired, it is imperative that the cause of the damage is known and eliminated at the start of the work in order to avoid consequential damage. If this is not the case, a leakage location is usually carried out first. With Heylo's range of moisture measurement technology, more than 90% of leaks are found within the shortest possible time.
Step 2 – Damage prevention through preparation
Cables and pipes should be well stowed and wet floors secured to avoid potential hazards such as electric shocks. Furthermore, the water supply should be stopped and the spread of hazardous substances prevented. The room's inventory should be salvaged or elevated if possible.
Step 3 – The drying process
The use of condensation dryers and fans prevents further expansion of the damage. As a rule, the damp surfaces will have dried sufficiently within the first three days to allow the hidden damage to cavities to be seen. If the water has penetrated materials for a long time, it will take longer to remove it again with the help of a dehumidifier. Basically, three factors have an important influence on the success of wall drying:
- The temperature
- The air humidity
- The air flow
Warm material naturally has a higher evaporation rate than cold material. In addition, warm air can absorb considerably more water vapour and carry it to the drying unit than cold air. The transfer of water vapour from the material to the room air is significantly improved by air flow. A fan should be installed in addition to every dryer set-up. At temperatures below 15°C, dryers should be operated with the support of heaters.
In case of strong partial moisture penetration, a targeted air flow to the component by means of a fan or heating by means of infrared heating plates, such as the infrared heating plates Trotec TIH 650+, leads to faster drying. Especially with very wet aerated concrete, the silent heating plates and blowers deliver convincing results.
Step 4 – Monitoring the drying process
Measurements are taken throughout the drying process to monitor and document the drying progress in the material. This is generally done in a systematic rhythm. To avoid unnecessary travel times, there are nowadays internet-based systems for remote retrieval of measured values. Complete documentation is very important for evaluating the drying progress and as proof for later purposes. A measurement protocol is created for all measurements. The most important measurement methods for documenting the drying progress are as follows:
- Resistance measurement: Exact wood moisture measurement.
- Measurements are taken during the entire drying process to control and document the drying progress in the material. Complete documentation is very important for evaluating the drying progress and as proof for later purposes.
- Resistance measurement: Moisture measurement in building materials with a depth probe. Resistance measurement is used to measure the moisture content of materials in deeper layers, such as screed insulation layers, with the 4-in-1 moisture meter MMS 2.
- Capacitive measurement: The search mode for finding damp spots. Where even the smallest measuring holes are taboo, the moisture below the surface can be located capacitively with non-contact measuring devices, such as HFM 200.
- Humidity and temperature measurement: Measurements in the room or cavity. Precise measuring devices with or without data storage and evaluation are used to test and document room air temperature and relative humidity, such as the Hygromaster 2 or MMS 2.
Step 5 – Dismantling
Degradation can begin as soon as comparative measurements show that the outgoing air has the same moisture content as the dry air blown in. In addition, the measured values of the material moisture of accessible building components should correspond to the comparison values in order to prevent further moisture damage.
Costs and duration of water damage drying
Drying with condensation dryers is the most efficient method, as the energy costs remain manageable and the drying times are considerably shorter. The dehumidifier DT 760 is the optimal device for acute emergencies such as water damage and works in cost-saving and quiet operation. In combination with fans, technical drying is even more effective. The use of fans accelerates evaporation, which can shorten the drying process by up to 50%.
A drying time of 14 days should be allowed for the drying of solid masonry. However, the actual drying times depend on the material involved, the structural design of the part of the building and the amount of water absorbed. In addition, the proper construction and the appropriate use of equipment for technical drying are decisive.
Drying water damage with Heylo equipment
In today's construction methods, floors contain an insulating layer into which moisture penetrates in the event of water damage. Screed insulation drying reduces the risk of long-term damage. There are two methods for drying the screed:
- Overpressure method
- Negative pressure method
In the overpressure method, dry air is forced into the insulation layer by means of a side channel compressor and exits via the edge joint or via relief holes. With the negative pressure method, the exit can be controlled, as dirt does not enter the room in an uncontrolled manner. Here, the air is extracted from the screed insulation layer by means of a side channel compressor and can be discharged into the room or outside through special HEPA filters such as the HFB 600. If there is free water in the insulation layer, a water separator must be connected upstream of the side channel compactor in this method. This is where a professional water damage drying dehumidifier such as the HWA 600 water separator comes into play.
For both processes, adsorption dryers and correspondingly dimensioned side channel blowers such as the SKV 115 are preferably used. With a side channel blower from Heylo, drying can be carried out in a pressure and suction process. Water and residual moisture are thus removed. In this process, the air is extracted from the insulation layer by means of a side channel blower (SKV) and can be discharged into the room or to the outside through special HEPA filters such as the HFB 600. However, suitable measures must be taken to ensure that no water or solids can get into the side channel blower and damage it. If there is free water in the insulation layer, a water separator must be connected upstream of the side channel blower with this method. This is where Heylo's professional water separator HWA 600 comes into play. It pre-cleans the sucked-in dirty air so that no solids or water can get into the SKV.
In principle, the topic of mould or artificial mineral fibres (KMF) requires special attention in this context. It is not uncommon for mould spores and KMF to be spread throughout an entire building as a result of careless "renovation work". Areas that were not originally infested were thus unnecessarily contaminated. The targeted use of air purifiers with HEPA filters and suitable disinfectants are another way to contain consequential damage.
FAQ on drying in case of water damage
How long does the process take?
Technical drying should be carried out by a qualified water damage restoration specialist. If heating and ventilation are not enough, more elaborate measures must be taken with special drying equipment, which can take up to 14 days. Here, the specialist company plans the right drying method and properly dimensions the number of drying devices. They can also estimate any gutting and disinfection measures that may be required.
Water damage – who pays for the drying?
There are various insurances for water damage that can pay for the damage:
- The occupant's household insurance pays for water damage to movable furniture.
- The owner's building insurance pays for all damage to the building. It also pays for the repair and restoration after the water damage.
- The causer's private liability insurance pays for damage to other people's furniture and buildings.
- Natural hazard insurance pays for damage caused by natural events such as heavy rain or floods.
Doing water damage restoration yourself?
Building drying or water damage restoration should not be started without professional knowledge and expertise. In this case, it is advisable to commission a specialist company to carry out the water damage restoration.
For more information on Dantherm Group dehumidifiers and water damage restoration solutions contact the team.
Related products
Featured insights
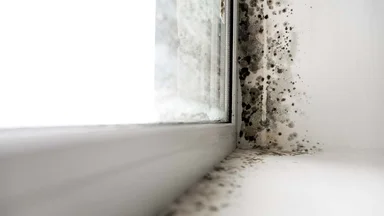
Everything you need to know about mould and mould removal.

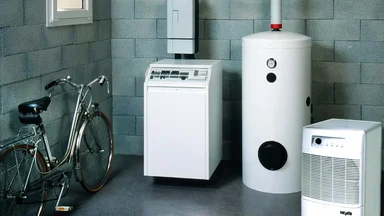
Find out how to dry out damp basements and cellars.

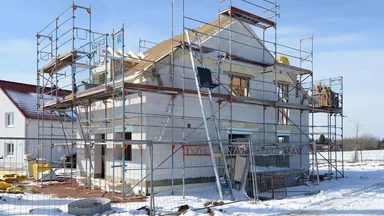
Instant space heating for construction workers in the winter months.

Need help with choosing the right solution? Our team of over 100 climate control experts can assist.
You can also reach out or join the discussion on our Social Media. Check out our LinkedIn page.