Improving heat safety in production facilities
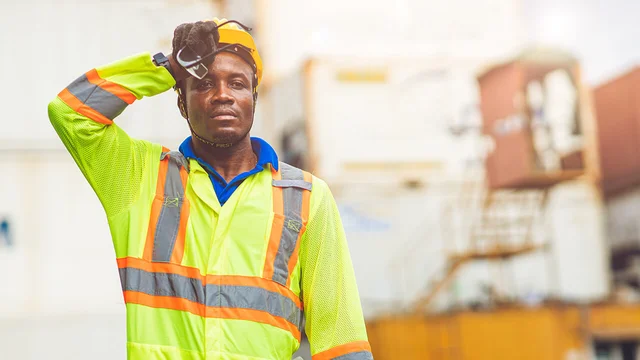
- Home
- Insights
- Cooling insights
- Improving heat safety in production facilities
In this article, we explore the dangers of excessive heat in the workplace and why staff in industrial production facilities are particularly susceptible. We’ll also be looking at some of the challenges that employers need to overcome in order to comply with strict heat safety regulations.
High temperature, high risk
The facilities that first come to mind when we think of safety concerns surrounding high temperatures are in heat intensive environments like steel and glass manufacturers or baked goods production – in each of these cases, ovens and furnaces are an integral part of the process.
However, hot summer months, old buildings with poor insulation and physically intensive labour can leave any kind of production facility susceptible to rising temperatures, creating dangerous working conditions. Some of the things that make these environments so difficult to cool include:
Large open spaces
To accommodate equipment, production lines and materials, many manufacturing facilities have high ceilings and a large floor area. All this open space takes extra time and energy to cool down.Moving parts
In a busy production facility, staff and machinery (such as forklifts) need to be able to move about throughout the day, unhindered by fixed ducts, fans or bulky cooling units.Old buildings
While modern constructions need to meet certain environmental requirements, older buildings, not designed for today’s intensive workloads, have little or outdated insulation. In hot climates, this means that indoor temperatures quickly rise and cold air will easily escape.Manufacturing processes
New technologies have been instrumental in boosting productivity. However, many of them also use intensive heat that, when left unmanaged, will add to the temperatures inside a facilityVentilation
Unlike an office, which can be relatively well-sealed to maximise cooling efficiency from air-conditioning, production facilities need enough ventilation to remove the dust, chemicals and contaminants produced during manufacturing process.
Why workplace temperature is a hot topic
In a previous article, we covered the detrimental effects that high temperatures can have on productivity for manufacturers across the globe.
And on top of that, governments and unions are also mounting more pressure on employers to provide safer and more comfortable working conditions for staff, especially in regards to heat safety.
Now, more than ever, finding efficient cooling solutions is of paramount importance.
How heat affects the body
The level and speed at which temperatures rise in a production facility will determine the symptoms and severity of overheating in the workplace. Some of the most common and most dangerous heat related illnesses include:
Heat Syncope
Usually caused by standing for a prolonged period of time or suddenly rising from a sitting position, the symptoms of Heat Syncope include light-headedness, dizziness, and fainting.Heat Cramps
When excessive sweating depletes the body’s salt and water levels, painful cramps can occur in the muscles used during physical work – most commonly the arms, legs and torso.Heat Exhaustion
Often a warning sign of Heat Stroke, the symptoms of Heat Exhaustion include headaches, nausea, dizziness, fatigue, weakness, thirst, heavy sweating and irritability. It is often accompanied by elevated core body temperatures around 38°C-39°C.Heat Stroke
Confusion, clumsiness, slurred speech, fainting/unconsciousness, hot dry skin, profuse sweating, seizures, and a high body temperature are all symptoms of Heat Stroke; the most serious heat-related illness in this list. It occurs when the body becomes unable to adequately dissipate heat and loses the ability to regulate core body temperature. Heat stroke can cause permanent disability or death if emergency medical treatment is not given promptly.
It’s important to remember that different people react differently to high heat levels. Personal risk factors such as lack of physical fitness, existing health conditions and previous episodes of heat-related illnesses all need to be accounted for by employers.
The dangers of heat go deeper than you might think
It’s an unfortunate truth that even with comprehensive training, strict safety measures and modern equipment, accidents in production and manufacturing facilities are a relatively common occurrence.
In fact, according to Reporting of Injuries, Diseases and Dangerous Occurrences Regulations (RIDDOR), the manufacturing sector reported about 66,000 non-fatal injuries in the UK alone throughout 2020.
Some of these could be broken down into:
Slip, trip or fall – 23%
Lifting/carrying – 22%
Struck by a moving or falling object – 13%
Contact with machinery – 12%
(Source: HSE)
Looking at a production facility’s accident report at first glance, incidents like those above are often listed as the primary cause. For example, when incidents of fainting (one of the most common effects of overheating) are simply reported as “fainting”, employers have no insight into what might have been behind it.
To put this into some context, research by NASA (also cited in our article on productivity) showed that mistakes and errors increase exponentially with rising temperatures.
Effective Temperature: | 24 | 26 | 29 | 32 | 35 |
Error Rate Increase: | 0% | 5% | 40% | 300% | 700% |
Without taking the effects of rising temperatures into account, employers are missing an integral part of the story, and therefore the information they need to make their workplace safer for staff.
Finding the most efficient solution
Under Occupational Safety and Health Administration (OSHA) law, employers are responsible for making sure that workplaces are free of known safety hazards. This includes protecting workers from extreme heat by implementing safety measures such as:
Fans to circulate air around the building
Enforcing more regular breaks as temperatures rise
Introducing flexible working patterns to limit heat exposure
Ensuring doors and windows can be opened for sufficient ventilation
Placing insulation around hot pipes
Installing air-conditioning
Situating workstations away from direct sunlight or heat-emitting machinery
In principle all, or a combination of these solutions, are ideal. But in reality their efficiency relies on building type/configuration, manufacturing processes and the type of work being carried out in a facility. This means that they may not always be practical in terms of cost, energy usage or cooling efficiency. And, in many cases, they simply won’t be possible to install.
While ensuring safety and comfort for workers should always be the top priority, employers can’t ignore the fact that the solutions they put in place to meet regulations will have an upfront cost and an impact on productivity and overall output.
How to solve the cooling issues in industrial production
Evaporative cooling systems have the flexibility to cool any part of a production facility with little or no installation, no extra ducting and without impeding daily operations.
Evaporative cooling systems take advantage of a natural process to cool down a space. As water evaporates, particles with the highest energy leave the moisture first, leading to a drop in temperature.
A fan draws hot dry air across cooler pads which absorb water from a reservoir.
When the hot air crosses the cooler pads, the water molecules on the surface evaporate and lower the air temperature inside the system.
This fresh air is circulated around a building, forcing hot stale air outside.
Key benefits for industrial production
With the right system and a strategic set up, evaporative cooling can help manufacturers meet the heat safety regulations required of their facilities while maintaining productivity.
Cooling efficiency
As water evaporates, particles with the highest energy leave first, causing the temperature to drop. This means that the warmer the air in a space, the more water can be evaporated, and the more effective the system becomes.
Convenience
While buildings need to be relatively well sealed for air-conditioning to be effective, evaporative cooling units can operate at maximum efficiency while doors and windows remain open.
Simplicity
Even the most advanced evaporative coolers are based on scientific principles that have been in use for centuries. So as well as a relatively low up-front cost, they are incredibly easy to use, install and maintain.
Practicality
When it’s only necessary to cool areas where work is taking place, portable evaporative coolers can be used for ‘spot cooling’. This means that cool air can be directed exactly where you need it.
Cooled recovery zones
When the space and configuration inside a building makes even portable units impractical, evaporative coolers can be used in staff rest areas to increase comfort and help them recover faster.
Low energy usage
By using energy already present in the process of evaporation, evaporative air coolers use up to 80% less energy than standard air-conditioning.
Air quality
Because fixed evaporative cooling units can use fresh, natural air from outside the building, fumes, odours and stale air can be eliminated instead of re-circulated.
With Master’s portable and fixed evaporative cooling solutions, not only are you getting the best quality equipment, but also the expertise to match.
Our team will offer advice on choosing the most appropriate unit for your facility, take care of any installation, train your employees on getting the best from it and can provide routine maintenance when needed. Get in touch via the contact form below to find out more.
Related products
Featured insights
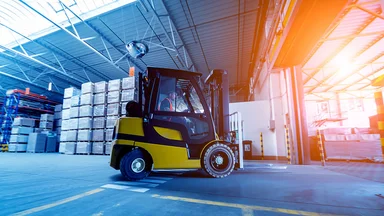
Why we recommend evaporative air cooling

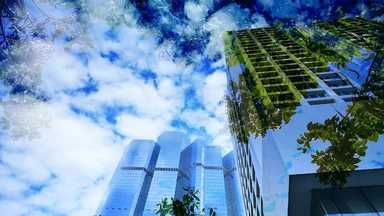
Learn the main differences and why evaporation is often a better choice

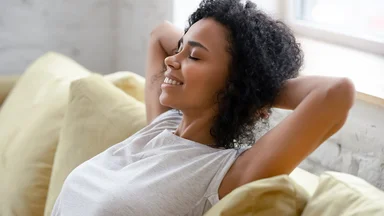
A natural alternative that delivers clean air using less energy

Need help with choosing the right solution? Our team of over 100 climate control experts can assist.
You can also reach out or join the discussion on our Social Media. Check out our LinkedIn page.