The best mobile dehumidifier setup for water damage restoration
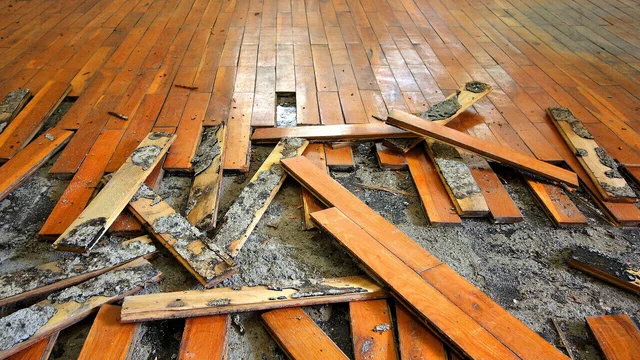
- Home
- Insights
- Humidity control and drying insights
- The best mobile dehumidifier setup for water damage restoration
Flooding, severe weather conditions, burst pipes, poor DIY attempts, and the after effects of fire fighting… There are a variety of reasons for water damage in buildings, each needing their own approach when it comes to drying and restoration.
For homes and commercial buildings, water damage can be devastating. But with a trained technician and the right dehumidification set-up, it’s amazing how well a building can be restored to its original pre-loss condition.
What happens to a building affected by water damage?
Inherent structural defects can become unsafe
Rooms can become a breeding ground for mould, bacteria and viruses
Construction materials can warp and decay
While the tools and specific drying methods used should be bespoke to the severity of damage and the type of building affected, water damage restoration normally follows three initial stages.
1. Moisture measurement and mapping
The first and most crucial stage of drying any building, moisture measurement and mapping normally involves a site visit to analyse the extent and severity of the water damage. This enables the technician to:
Identify the root cause of the water damage (which isn’t always as obvious as you might think)
Determine the type of construction, insulation and materials that have been affected
Begin to compile accurate documentation for tracking the drying progress
2. Stabilisation
This stage minimises the risk of secondary damage to the building while other restoration work takes place. It typically involves:
Asbestos checks
The use of a condensing dehumidifier to reduce the risk of mould and condensation forming by keeping relative humidity (RH) levels below 60%
The installation of an air filtration device to help remove dirt, bacteria and mould spores from the atmosphere, where deemed necessary
3. Structural drying
Before deciding on the most appropriate drying method, the technician will analyse how the structural elements of a building have been affected. To determine the most damaged areas, they will make a comparison against their initial moisture mapping by retaking measurements including:
Wood Moisture Equivalent (WME)/Wood Moisture Content (WMC)
In-depth humidity/Equilibrium Relative Humidity (ERH)
Relative scale (REL)
Non-invasive measurements (capacitive measurements)
Surface Temperatures/Thermal Imaging
Choosing the best solution
After completing these essential checks, it’s time to decide on the most effective dehumidification configuration and determine the right methods for the job, such as:
Condensation drying and air movement
This is the most widely-used method for addressing water damage to buildings with plasterboard walls and ceilings, lightweight concrete blocks and wooden framing. It works best in warm to medium climates and delivers excellent energy efficiency.
For colder temperatures, solutions with built-in 1kW heaters and high pressure fans can be used to warm up the damaged areas and speed up the drying process.
Adsorption drying
For especially cold climates and more difficult to dry building materials like hardwoods, dense concrete and insulation, adsorption drying is a top contender.
By flowing the damp ambient air through a desiccant material, such as a silica covered rotor, it’s a method that can achieve relative humidity (RH) levels up to 20% lower than a more traditional refrigerant-based drying system.
Pressure and suction drying
With the increasing use of more sustainable, eco-friendly materials like non-permeable membranes, open/closed cell insulation as well as vapour retardant coatings, new challenges are presented for water damage restoration.
Systems like the Aerial AERCUBE that apply both positive and negative pressure, can guide warm dry air into the hard to reach areas of multi-layered buildings. The AERCUBE system, in particular, can also be configured and streamlined to make it a bespoke tool for every job. See how it works in the video below.Heat drying
A relatively new method of water damage restoration, heat drying is incredibly effective when air and surface temperatures are very low and a building’s central heating system is inaccessible.
However, one of the main benefits of this solution is that it gives you the ability to target and control heat levels in specific areas — focusing high amounts of energy to the most affected parts of a building.
Remote monitoring
The ability to keep track of the drying progress of a water damage restoration project without having to be on site is a huge benefit in terms of cost, time and project management.
This allows you to make sure that your equipment is working at top performance and provides you with indicators that help predict when the drying is complete so you know when to plan to decommission your system. These systems do not just provide data, they can also provide remote control over your drying solutions.
Looking for a solution that covers all scenarios?
With a range of mobile dehumidifiers, including the customisable AERCUBE, Aerial are one of Europe’s leading solutions for drying out homes and commercial buildings after flooding and water damage. To learn more, get in touch to speak with our team.
Related products
Featured insights
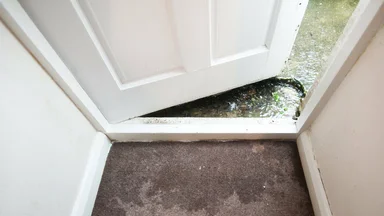
Expert advice for your next project

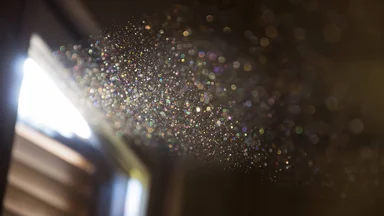
What to do when the atmosphere becomes a hazard

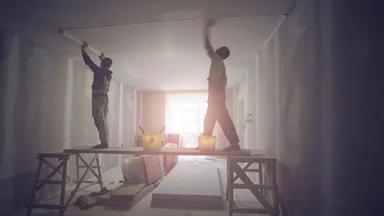
Keep your building timelines on track.

Need help with choosing the right solution? Our team of over 100 climate control experts can assist.
You can also reach out or join the discussion on our Social Media. Check out our LinkedIn page.